通过实验优化洗涤塔性能,需围绕净化效率、能耗、稳定性三大核心目标,结合单因素实验、多因素正交 / 响应面实验、动态运行测试等方法,系统探究关键参数对性能的影响规律,最终确定最优运行条件或结构设计。 通过实验优化洗涤塔性能,需围绕净化效率、能耗、稳定性三大核心目标,结合单因素实验、多因素正交 / 响应面实验、动态运行测试等方法,系统探究关键参数对性能的影响规律,最终确定最优运行条件或结构设计。以下是具体实验优化思路与步骤: 一、实验设计前的准备 明确优化目标与评价指标 核心指标:污染物去除效率(如 SO₂、粉尘、VOCs 的去除率)、压力损失(能耗)、液气比(L/G,影响运行成本)、长期运行稳定性(如阻力变化、喷嘴堵塞情况)。 辅助指标:喷淋液 pH 值变化、雾滴夹带量、废液污染物浓度(评估二次污染风险)。 确定关键影响因素 根据洗涤塔类型(如填料塔、空塔、板式塔)和处理对象,筛选需优化的参数,常见因素包括: 操作参数:进气流量(气速)、喷淋量(液气比 L/G)、喷淋液浓度 / 温度、进气污染物浓度。 结构参数:填料类型 / 高度、喷嘴类型(空心锥 / 扇形)/ 布置密度、塔径 / 塔高比、除雾器类型。
二、分阶段实验优化方案 阶段 1:单因素实验 —— 筛选参数敏感区间 通过控制单一变量,固定其他条件,探究该因素对性能的影响趋势,确定关键参数的合理取值范围(避免后续多因素实验范围过大)。
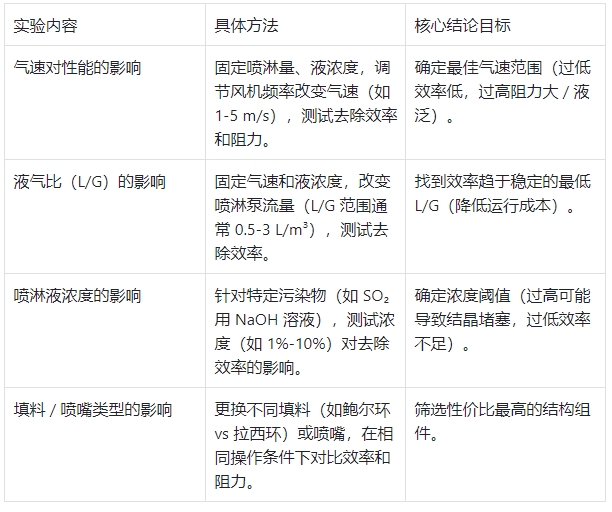
示例:处理含尘废气时,单因素实验可发现:气速从 1 m/s 增至 3 m/s 时,粉尘去除率从 60% 升至 90%,但气速超过 4 m/s 后,阻力急剧上升(因液泛),故初步确定气速合理区间为 2-3 m/s。 阶段 2:正交实验(适用于参数较多时的快速筛选) 选择 3-4 个关键因素(如气速、液气比、喷淋液浓度、填料高度),每个因素设 3-4 个水平(基于单因素实验的敏感区间),设计正交表(如 L₉(3⁴) 表),减少实验次数。 示例:针对填料塔脱除 SO₂,因素与水平可设为: 气速:2 m/s、3 m/s、4 m/s 液气比:1 L/m³、2 L/m³、3 L/m³ NaOH 浓度:2%、5%、8% 通过实验结果的极差分析或方差分析,确定各因素的影响权重(如液气比 > 气速 > 浓度),并筛选出较优参数组合(如气速 3 m/s、L/G=2 L/m³、浓度 5%)。 响应面实验(适用于高精度优化) 针对 2-3 个关键因素(如气速、液气比),在正交实验基础上,通过中心复合设计(CCD)增加实验点,建立 “因素 - 响应值(如去除效率)” 的二次回归模型,通过模型求解最优参数。 优势:可量化参数交互作用(如气速与液气比的耦合对效率的影响),并通过等高线图直观呈现最优区间。 阶段 3:动态运行与稳定性验证实验 通过长期连续运行实验,验证最优参数的稳定性,并评估设备的抗干扰能力(如进气浓度波动、长时间运行后的性能衰减)。 多因素交互实验 —— 确定最优组合 单因素实验仅能反映单一参数的影响,而实际中参数间存在交互作用(如液气比与气速共同影响气液接触效率),需通过正交实验或响应面实验优化。
三、实验数据的分析与优化模型建立
1.数据可视化与规律总结 绘制 “因素 - 响应值” 曲线(如液气比 - 去除效率曲线),确定临界值(如效率不再提升的最低液气比)。 对多因素实验数据,通过方差分析(ANOVA)判断因素影响的显著性(P 值 < 0.05 为显著)。
2.建立优化模型 基于实验数据,拟合经验公式(如去除效率 = f (气速,液气比,浓度)),或通过机器学习(如神经网络)预测不同参数组合下的性能,快速筛选最优解。
3.验证与迭代 将优化后的参数在实际装置中测试,若与实验结果偏差较大(如去除效率低 5% 以上),需补充实验(如考虑实际进气波动、设备磨损的影响),迭代优化方案。
四、典型场景实验案例(以填料塔脱除酸性气体为例) 1.目标:优化 SO₂去除效率(≥95%),同时降低液气比(减少能耗)。 2.关键因素:气速(2-4 m/s)、液气比(1-3 L/m³)、NaOH 浓度(2%-6%)。 3.实验结果: 单因素实验显示:液气比增至 2 L/m³ 后,去除效率趋于稳定;气速超过 3.5 m/s 时阻力骤升。 正交实验发现:液气比(2 L/m³)、气速(3 m/s)、浓度(4%)组合时,效率达 97%,且阻力适中。 连续运行 100 小时后,效率下降至 93%(因溶液 pH 值降低),故优化方案增加 “pH 在线调节”(自动补加 NaOH,维持 pH=8-9),最终稳定效率达 96%。 通过系统化实验,可精准定位影响洗涤塔性能的关键参数,实现 “高效、低耗、稳定” 的优化目标,同时为工程放大(如从实验室小试到工业中试)提供可靠数据支撑。
|